Our Process
We apply our knowledge and experience to create a one-of-a-kind design that fits your lifestyle, budget, and building site.
As a first step, we need to get a good understanding of the home that you are trying to create. Since each structure is custom designed, we want to know the details of the building site as well as your own personal requirements and expectations. Using information about your building site specifics (topographic info, views, solar exposure, access, etc.) paired with your spatial requirements, we can establish a size and configuration to best fit your needs. From there, we will run a complete cost analysis for you. We will be able to give you the cost for the components that we provide (design and engineering, as well as the structural, waterproofing, and ventilation systems). We can also provide you with estimates on flat work and shotcrete for the shell. Our goal is to give you a very good idea of the scope of the project and the associated costs before we start on your set of floorplans.
Design and Engineering
We will provide you with a custom, complete set of floorplans. A set of Formworks floorplans includes elevations, foundation, floor framing, structural cross sections, steel framing, electrical and mechanical details. Plans are priced at $1.25/sf. Plans will be reviewed and certified by a structural engineer for an additional cost. Engineering certification fees may vary from state to state. Rates typically range from $1,500.00 to $2,500.00. depending on the size of the structure and the complexity of the design.
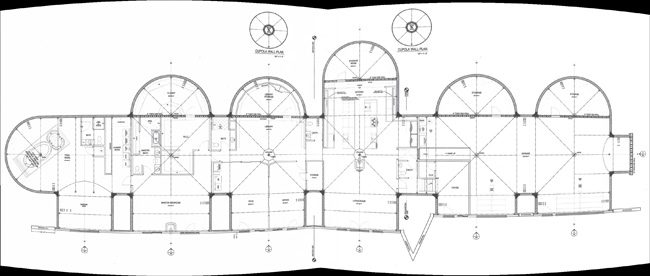
Formworks’ patented building system consists of 4 primary components: Structural Steel, Shotcrete, Waterproofing and Whole House Ventilation Systems.
1. Structural System
Our system is designed to give the builder confidence in constructing one of the most technologically advanced structures in existence. The structural skeletal steel is a pre-fabricated, easy to assemble bolt together system that is designed to be erected by any labor crew. The steel I-Beams control the shape of the structure, the spacing and attachment of the reinforcing steel and provides the primary forming strength.
The Formworks structural system includes:
- foundation anchor plates and rebar receiving tubes
- main structural steel beams
- bolt in place floor support tubes
- all nuts and bolts for the steel frame
- reinforcing steel (rebar) for the shell
- forming system
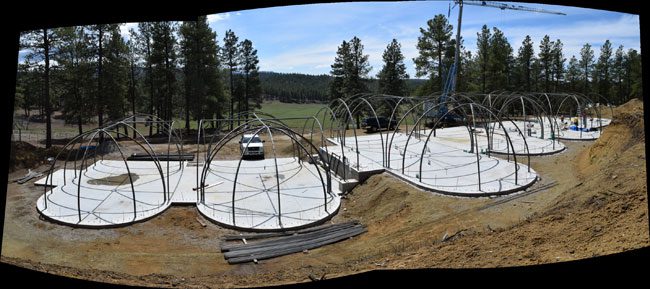
A Formworks structure takes the same amount of time to construct as a similar sized conventional building. The building system controls the structural elements and makes building simple, thus faster and less expensive to complete. Every piece of steel arrives on site, marked for simple installation. The primary steel is bolted together and lifted into place either by lifts or manually. Once the steel beams have been erected, the rebar is ready to be installed. The outer flange of the steel has rebar receiver tabs already welded into place. The horizontal rebar is simply placed in the open end of the tab, creating the correct placement and spacing, eliminating any guesswork for the builder. Continuing the rebar from tab to tab around the perimeter of the structure creates the frame of the building.
Once the rebar is in place, a high density foam liner is attached to the interior steel of the structure to serve as both form and backstop for the shotcrete process.
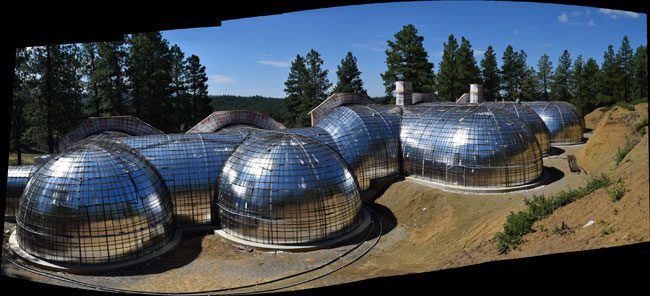
2. Shotcrete
Shotcrete is pneumatically placed concrete sprayed under pressure through a hose and delivered through a nozzle. The same process is used to create concrete swimming pools. The shotcrete is applied from the exterior, which makes the job common work for any shotcrete crew. A well-organized shotcrete crew is usually in and out in a day or two, depending on the size of the project.
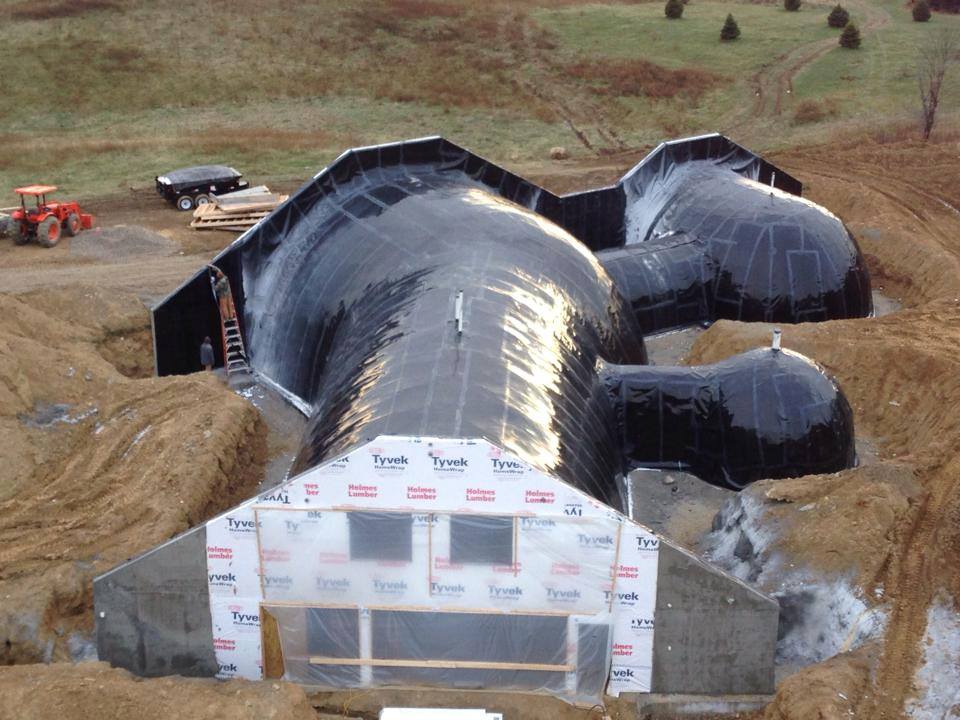
3. Waterproofing System
Critical to waterproofing are the products used in combination to create a complete and proper protective system for your Formworks structure. This system is a multicomponent water barrier system. The components of this system can successfully be installed by the homeowner and/or labor crew with assurance. It is a true waterproofing that is applied directly to the exterior concrete surface.
The main component of our waterproofing system is designed for use below-grade and is a dual layer waterproofing consisting of HDPE, sodium bentonite, and a protective layer consisting of a non-woven polypropylene. The HDPE provides the first layer of waterproofing while the bentonite’s self-sealing capabilities ensure positive puncture protection under hydrostatic conditions.
Accessory components that will be used in conjunction to the membrane:
- Cold-Joint Water-Stop applied between the footing and the shell wall
- Seam Tape will secure the membrane and provide continuous protection
- Termination Bar will secure the membrane at grade
Once the waterproofing system has been installed, the high-density foam boards that were initially used as the backstop for the shotcrete process, will now be relocated to the exterior of the structure to act as backfill protection board. This will eliminate the need and the associated costs with importing a select fill material to backfill the structure. The earth that was excavated out in preparation for the foundation/slab, will be reused to cover the structure once complete. The foam boards will also provide the exterior shell walls with additional R-value, increasing the overall energy efficiency.
Depending on the specific building site location, an umbrella system may be utilized; incorporating a drain mat that will be placed in addition to the waterproofing membrane. The drain mat combines geotextile filter fabrics with specially designed drainage cores that will insulate the mass of the earth surrounding the structure. Excess ground water will be shed away from the structure as well as the surrounding earth. The soil surrounding the home is kept dry, minimizing the effects of soil temperatures around the structure. The result is a comfortable indoor temperature that varies only six or eight degrees during an entire year, while outdoor air temperatures may vary from minus 40 to more than 100 degrees F.
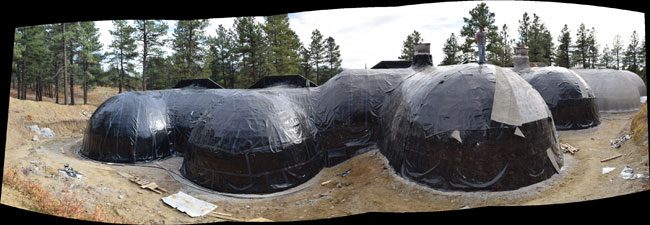
4. Ventilation System
Formworks’ residential and commercial structures are extremely airtight and because of this, a ventilation system is designed into each of our designs. Unlike ordinary ventilation systems, our system handles both exhaust and fresh airstream while also moderating temperature extremes and humidity in both summer and winter.
Homes in different parts of the country face a wide range of temperature and humidity conditions. Energy Recovery Ventilators moderate extremes in outdoor temperature and humidity. Since ERVs have both an exhaust fan and a fresh air supply fan, it is pressure balanced and is the ideal year-round, whole house approach to efficient and effective ventilation.
In the winter, that means that the cold, dry outside air is preheated and humidified by the outgoing warm interior air. And in the summer, the warm, humid outside air is precooled and dehumidified by the outgoing air-conditioned interior air.
How it works:
The simple yet effective cross-flow technology provides positive air stream separation. The innovative static-plate core (manufactured by RenewAire) composed of multi-layered leading-edge hydroscopic resin plates, is designed to prevent fresh incoming air from ever mixing with what’s being exhausted to the outdoors. At the same time, the ERV system transfers both heat and water vapor into or out of the incoming fresh outdoor air, moderation winter/summer temperature and humidity extremes year-round.
Just as important, the ERV helps protect occupants from harmful indoor pollution like CO2, smoke, formaldehyde, VOCs, and radon by allowing an adjustable and efficient exchange between intake and exhaust.
- Replaces noisy and inefficient bathroom exhaust fans
- Small duct work system to collect air form each exhaust location
- Optimal automatic proportional runtime control panel and push button controls in each exhaust location (bathrooms, laundry room, utility room, etc.)
- High-efficiency core operates dry in all conditions, meaning no condensate pans or drains are needed